CONCRETE JOINTS: 2 COMMON TYPES AND THEIR PURPOSES
- By Southport Concrete Corp.
- •
- 20 Jul, 2018
- •
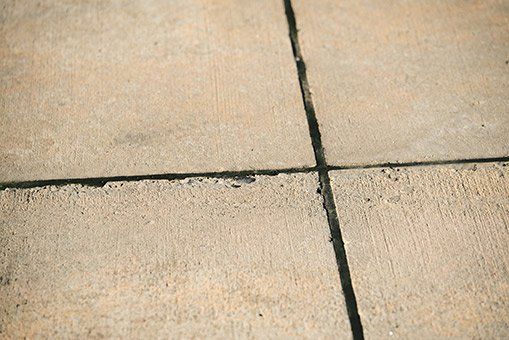
As you are surely already aware, concrete is one of the best materials for constructing residential features such as driveways, sidewalks, and patios. Yet not all concrete stands the same chances of success. Unless properly protected against, natural cycles of expansion and contraction can lead to the formation of problems like potholes, cracking, and spalling.
Fortunately, a professional concrete installation company knows that the likelihood of such problems can be greatly reduced through the use of concrete joints. If you would like to learn more about what such joints consist of, as well as how they can protect a concrete surface, read on. This article will outline two of the most frequently implemented types of concrete joints.
Contraction Joints
Contraction joints aim to reduce the occurrence of a common problem known as plastic shrinkage cracks. Such cracks develop as the concrete cures. During this process, water evaporates from the surface of the concrete. This leads to uneven hydration levels within the slab-a scenario that, in turn, leads to the formation of myriad small cracks as the upper portion of the concrete contracts.
Plastic shrinkage cracks are primarily a cosmetic concern, and shouldn't affect the overall stability of the concrete slab. Yet they can be quite unsightly, and will certainly devalue both the appearance and the long term value of the concrete. For that reason, it is vital to combat shrinkage cracks through the installation of contraction joints.
Everybody who has ever walked down a city sidewalk is already familiar with contraction joints, whether they realize it or not. That's exactly what those regularly spaced "cracks" are. A contraction joint acts to relieve shrinkage stresses by allowing the surface of the concrete to deform slightly without cracking.
A contraction joint must be cut in the concrete while it is still wet, using the tool known as a concrete saw. In order to be effective, such joints must also be deep enough. The rubric commonly used here is that the joint's depth must be at least ¼ the depth of the slab itself. If the joint is too shallow, it won't be able to adequately compensate for the shrinkage forces.
Expansion Joints
Cracks don't just form during the concrete curing process. Even once fully dry, it is possible for cracks to virtually destroy a concrete slab. Such cracks are most commonly caused by water. To understand why this is the case, it is helpful to realize that concrete is by nature quite a porous substance.
What this means is that concrete is great at absorbing moisture. This includes not just liquid water, but also moisture latent in the very air. As concrete soaks up such moisture, it's volume swells. The actual size change involved is quite small-a mere fraction of an inch. Yet this is more than enough to put a huge amount of internal stress on the concrete.
This is especially true when it comes to concrete that is installed directly next to a building, foundation, or other permanent structure. Because the concrete cannot expand outward, the internal pressure will cause cracks to form.
Expansion joints are the best way to allow concrete the little bit of "give" necessary to withstand hydration-related volume changes. Essentially, such joints involve the installation of a thin channel between the concrete slab and the neighboring structure. To prevent this groove from becoming filled with debris, it is usually filled with an easily compressed material like roofing felt.
Bottom Line
To ensure that a new concrete structure is able to live up to its promise, it is important that it be installed correctly. Concrete joints are one of the best ways to keep a concrete slab in good shape. For more information about how concrete joints work, and when they should be utilized, please don't hesitate to contact the experts at Southport Concrete Corp.
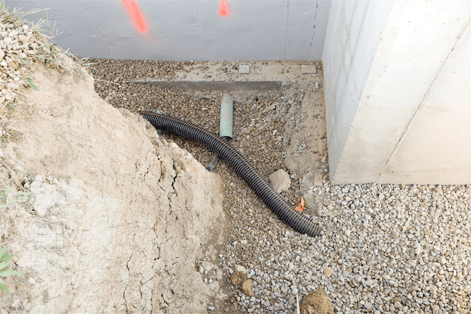
- Cost effective: When anything is manufactured on a massive scale, your costs decrease substantially from having something custom poured.
- Superior quality: Being pre-cast, pilings are checked for every sort of defect before being installed, giving them an additional safety advantage.
- Underwater usage: There are several instances in which the pouring of concrete in certain types of subsoil or other environments won’t set. The use of formed piles easily takes care of that issue.
- Convenience: With a wide selection of piles all ready to go, you are able to select what you need and install them at your convenience.
- Adaptability: Trying to pour the exact shape you need is a thing of the past with concrete pilings available in square, round, octagonal and other shapes.
- Incredible strength: Because of the nature of the piles, the reinforcement used inside is more likely to stay put without getting disturbed or moving its place. They also have high bending and lateral resistance to hold their strength in adverse conditions.
- Eco friendly: With no leftover materials to clean up at the installation site, piles are the most environmentally friendly option when supporting your foundation and in other applications, such as retaining walls, embankments and cofferdams.
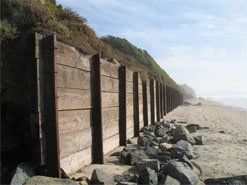
- Curved
- Vertical
- Mound
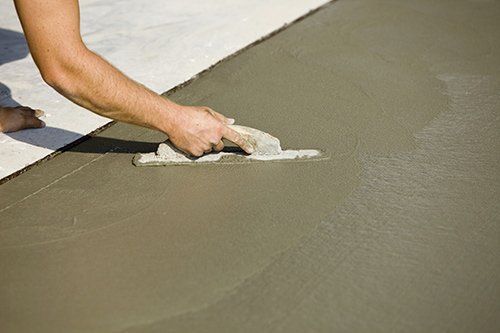
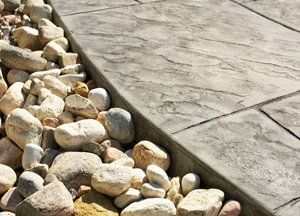
Although the terms cement and concrete are often used interchangeably, cement is actually an ingredient in concrete.
Concrete is basically a mixture of paste and aggregates. The aggregates are crushed stone or sand and gravel; the paste is made of water and Portland cement. Concrete material happens to get stronger as it gets older. Portland cement is not the name of a particular brand of cement; it’s the generic term for the type of cement utilized in almost all concrete (ex: stainless is a type of steel and sterling is a type of silver).
Pervious concrete, also known as "green concrete," is a choice that helps combat building code issues with storm water run-off.
Cement is composed of 10 to 15 percent of the concrete mix, by volume. Then through a process called hydration, the cement and water harden and bring together the aggregates into a rocklike form. This developing and hardening process continues for years, again meaning that concrete gets stronger as it gets older.
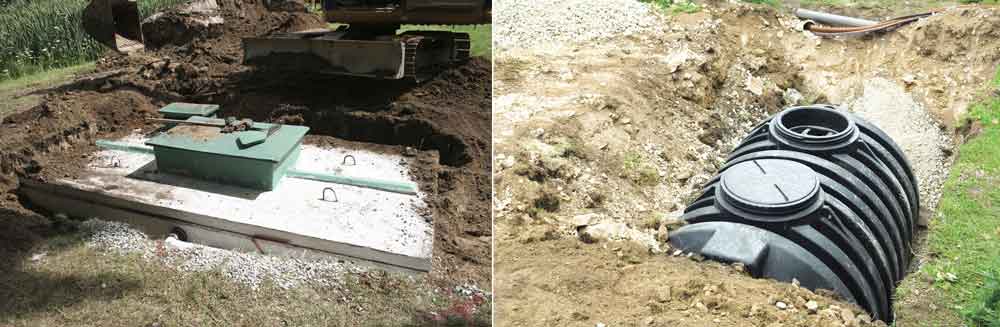
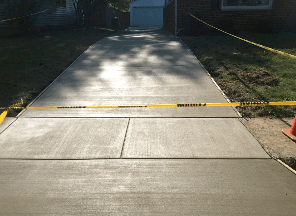
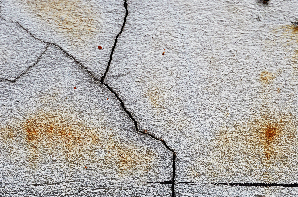
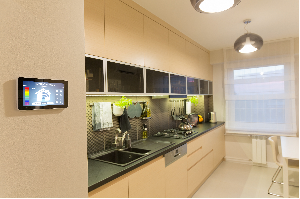
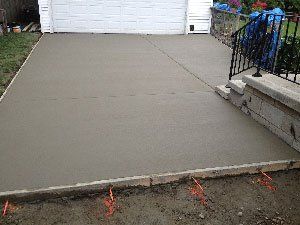