UNDERSTANDING POST-TENSIONED CONCRETE
- By Southport Concrete Corp.
- •
- 20 Jul, 2018
- •
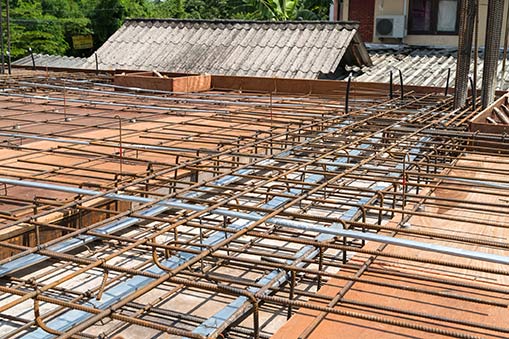
Once upon a time, a concrete slab was just that - a slab made up of concrete and nothing else. It didn't take long for contractors to learn that such slabs generally suffered from an unacceptable rate of cracking and other problems. In general, the thicker the slab, the more pronounced such issues were.
In an effort to increase the structural stability of poured concrete, a variety of different reinforcement methods were invented. Today the number of such strategies can be somewhat baffling - even for those who work in the industry. If you would like to brush up on your knowledge of concrete reinforcing techniques, read on.
This article will provide a useful overview of one of the most effective methods of reinforcing concrete: post-tensioning.
Installation Process
At the heart of a post-tensioning system lies a set of high tensile metal cables commonly referred to as tendons. Seven braded steel wires make up each tendon. These tendons are inside a corresponding number of plastic tubes. Installers lay these tubes, with the slack tendons inside of them, inside of the forms prior to the workers pouring the concrete.
The ends of the tubes must be oriented so that they lie flush along the inside of the forms. The idea is that concrete must be kept from getting into the tubes, lest it hardens and makes tensioning impossible. Once the concrete has cured to a fully hardened state - a process that can take days, if not weeks - workers move on to the stressing operation.
As its name would imply, the stressing operation involves the stretching of the tendons to the appropriate degree of force. Installers utilize hydraulic jacks to accomplish this. Most post-tensioned concrete is stressed to a value of 33,000 pounds of load. Once pulled to the appropriate degree of tension, the tendons anchor to the concrete's outer edge.
Prestressing
Post-tensioning as a form of concrete reinforcement falls under the larger category known as prestressing. This term can be somewhat misleading, leading many people to believe that the tendons are tightened prior to the workers pouring the concrete. Yet the pre in prestressing actually refers to the fact that tensioning occurs prior to any structural load that you place on the concrete.
Other types of prestressing techniques differ in that the reinforcing elements do have to be tensioned before the workers pout the concrete. By housing the tendons in plastic sheaths, however, post-tensioning allows workers to postpone this aspect until later in the installation. This simplifies the process, since tensioning the cables proves a much easier task once the slab has taken on its hardened state.
Benefits of Post Tensioning
The ease of the tensioning represents one of the chief benefits of post-tensioning. It allows workers to install concrete slabs more quickly and with less difficulty. The enormous strength of post-tensioned concrete also means that slabs do not need to be as thick as when using other reinforcing methods.
As a result, post-tensioned concrete allows contractors to lower their material cost by lowering the necessary volume of concrete. The incredible stiffness of post-tensioned concrete allows it to withstand structural instability in the underlying ground better. It also gives the concrete a greater degree of resistance to developing cracks. Any cracks that do manage to form will be pressed tightly together, making it difficult for them to grow or expand.
Concrete Experts
The advantages of post-tensioned concrete directly benefit those who work with concrete. Switching over from other prestressing techniques or rebar reinforcement makes more sense, the more you learn about posttensioning. For more information about this versatile concrete reinforcement technique, please don't hesitate to contact the pros at Southport Concrete Corp.
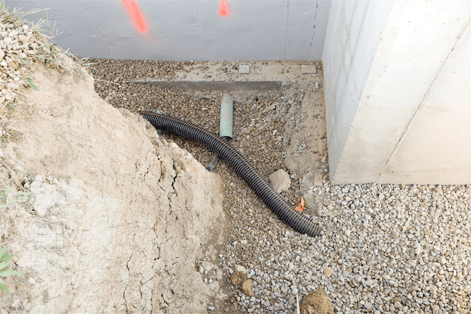
- Cost effective: When anything is manufactured on a massive scale, your costs decrease substantially from having something custom poured.
- Superior quality: Being pre-cast, pilings are checked for every sort of defect before being installed, giving them an additional safety advantage.
- Underwater usage: There are several instances in which the pouring of concrete in certain types of subsoil or other environments won’t set. The use of formed piles easily takes care of that issue.
- Convenience: With a wide selection of piles all ready to go, you are able to select what you need and install them at your convenience.
- Adaptability: Trying to pour the exact shape you need is a thing of the past with concrete pilings available in square, round, octagonal and other shapes.
- Incredible strength: Because of the nature of the piles, the reinforcement used inside is more likely to stay put without getting disturbed or moving its place. They also have high bending and lateral resistance to hold their strength in adverse conditions.
- Eco friendly: With no leftover materials to clean up at the installation site, piles are the most environmentally friendly option when supporting your foundation and in other applications, such as retaining walls, embankments and cofferdams.
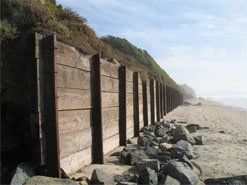
- Curved
- Vertical
- Mound
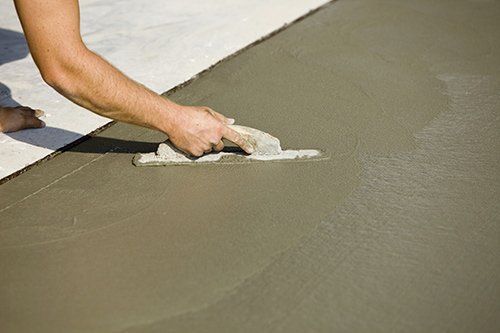
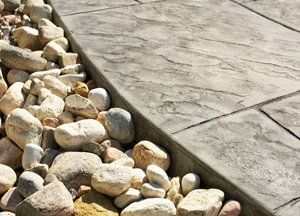
Although the terms cement and concrete are often used interchangeably, cement is actually an ingredient in concrete.
Concrete is basically a mixture of paste and aggregates. The aggregates are crushed stone or sand and gravel; the paste is made of water and Portland cement. Concrete material happens to get stronger as it gets older. Portland cement is not the name of a particular brand of cement; it’s the generic term for the type of cement utilized in almost all concrete (ex: stainless is a type of steel and sterling is a type of silver).
Pervious concrete, also known as "green concrete," is a choice that helps combat building code issues with storm water run-off.
Cement is composed of 10 to 15 percent of the concrete mix, by volume. Then through a process called hydration, the cement and water harden and bring together the aggregates into a rocklike form. This developing and hardening process continues for years, again meaning that concrete gets stronger as it gets older.
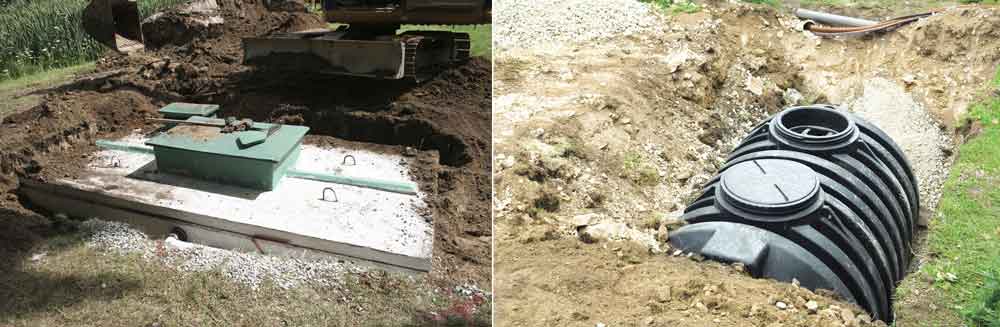
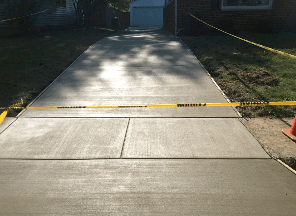
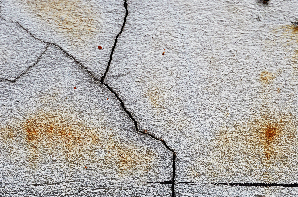
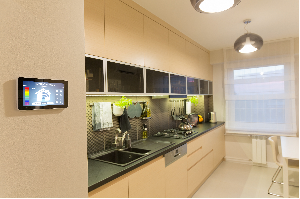
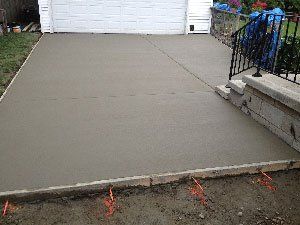